随着材料性能、设备及工艺水平的不断提高,使得越来越多的电子制造服务公司(EMS)不再满足于常规的smt贴装工艺,而不断尝试使用新型的组装工艺,这其中就包括倒装芯片(FC)。接下来,众焱电子小编将接着《倒装芯片与smt贴装工艺:焊料凸点倒装芯片工艺》一文中的内容继续讲解分析。
1、助焊剂的涂覆、贴装及回流焊
划片后从贴片环上取下芯片。目前尚没有传递裸芯片元件的工业标准,通常传递元件的方法有华夫式包装,冷凝式包装和长条带式包装。使用的贴装设备必须要与所使用的传递方法相容。华夫式包装适用于小批量或KGD芯片的传递,而长条带式包装则可以与现有的smt贴片设备很好地兼容,故而适用于大批量生产。
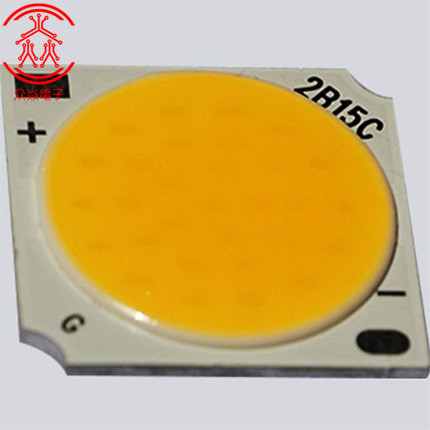
助焊剂的涂覆是FC组装工艺的第一个步骤。涂覆助焊剂的方法有很多,包括有喷涂法、点除法、浸渍法和模板印刷法。喷涂法是在贴装元件之前将液体焊剂雾化,并喷淋在贴装位置上。点涂法则是将助焊剂一滴滴点涂在己定位的元件底部。浸渍法使用旋转式涂覆机器,当元件位于焊剂涂覆机工作台时,为定位的方便,可将少量粘性材料沉积到凸点之上,该法适用于中等规模的批量生产。还需指出的是,不论使用那一种方法,所使用的助焊剂材料对涂覆工艺起着非常关键的作用。助焊剂必须具有足够的粘性,良好的润湿性以及尽可能少的残余物。
涂覆助焊剂即进行芯片的拾取和贴装。目前多采用高速的贴装及超高速的定位系统进行。影响贴装的主要因素包括有芯片的拾取,定位的准确性和可重复性,贴装头下压力的大小及时间等。定位的误差通常要求为焊球间距的10%。贴装头的顶部要根据传送类型、芯片的大小、焊料球的排布方式加以选择。为防止对芯片或焊料球造成不必要的损伤,顶部的硬度必须合适。
在smt贴片打样或加工过程中,为减少回流焊之前已贴装好芯片的移动,应尽可能地减少传递和运输。在后序的回流焊工艺中也同样要注意这一点。为保证焊点的质量,对回流焊时炉腔的气氛,工艺曲线要加以严格的控制。主要工艺参数包括有峰值温度,温度超过液相线的时间和降温速率。为防止基板的破坏,焊球处形成孑L洞等缺陷,最好是将热电偶直接置于芯片的下方,这样可以更精确地控制回流的温度。
2、下填充材料的充填
大部分下填料是在回流焊工艺之后进行,在某些情况下也可以在回流焊工艺之前进行。当然,不同工艺对下填料的性能要求也不相同,据此可将下填料分成两类:回流焊后下填充材料和回流焊前的下填充材料。由于前者要求所用的填充料具有一定的流动性,而后者则恰恰相反,所以也可将两者分别称作流动的下填充材料和不流动的下填充材料。
使用流动下填充料的常规填充工艺是利用装有填料的点胶机沿芯片的一边或两边施加填料,在芯片和基板之间缝隙的毛细管虹吸作用下,达到充填的目的。此时,充填的质量取决于芯片的尺寸和形状、缝隙的大小、焊点的排布方式,填充料的粘度以及填充料与芯片及电路板的润湿特性。其它工艺参数,包括点胶头的孔径,点胶头距芯片边缘的距离,距电路板的高度以及点胶的速度均会影响填充的质量。同时,为改善填料的流动性和防止其发生凝胶化反应,电路板的温度也是一个非常重要的工艺参数,工艺过程中也须严格控制。可通过C模式扫描超声显微镜(C-SAM)观察是否有孔洞和剥层,进而监控充填的质量。一旦在填充料与芯片和电路板之间形成剥层,将会导致应力集中,造成焊点过早破坏,特别是当环境潮湿或外界温差变化较大时。在其后的固化过程中,为充分发挥下填料的作用,对固化的温度、温度的均匀性、固化的时间以及炉腔内气氛等也要加以控制。
为了克服回流焊后下填充材料工艺过程较慢,同时与smt工艺不兼容的不足,人们开发了不流动的下填料。它可以在制造阶段预先施加在整个圆片上,划片后装配于整个基板上,填充料的固化和焊点的连接可在回流焊过程中一步实现。
3、结束语
当前约有1%的芯片是利用FC技术组装,但随着微电子及电子封装技术的快速发展,特别是与smt工艺相互结合后,FC终将会得到为迅速的发展并最终成为一种成熟的工艺技术。
广州众焱电子有限责任企业www.gz-smt.com,是一家专业从事SMT贴片加工、DIP常见加工、PCBA包工包料、PCB线路板制造的企业,拥有多年的电子加工经验,以及先进的生产设备和完善的售后服务体系。企业的SMT贴片加工能力达到日产100万件,DIP插件加工产能为20万件/日,能够给你提供优质的电子加工服务。